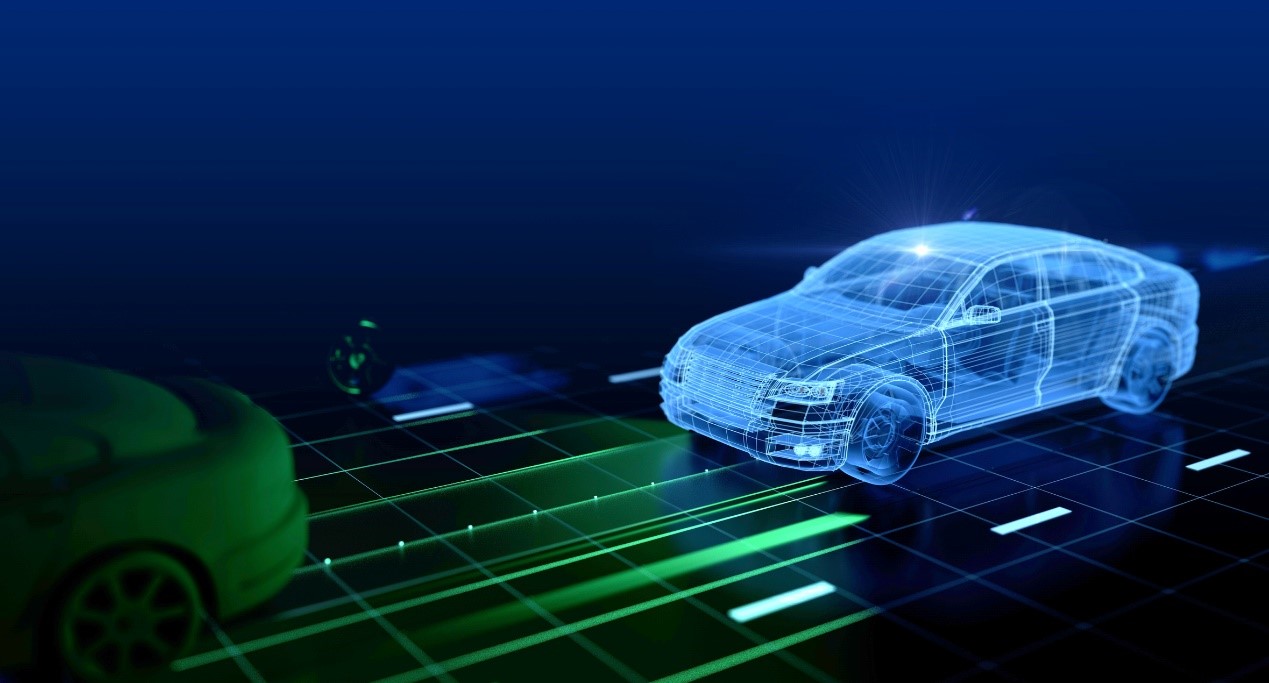
In the history of automotive development, aside from the evolution of power output, the most significant investment in research and development has been dedicated to providing drivers and passengers with more comprehensive safety protection. Initially, this focused on passive safety features such as airbags, seatbelts, and crumple zone design. With the rapid advancement from microcomputers to automotive computers, the focus shifted to active safety design, giving rise to the concept of Advanced Driver Assistance Systems (ADAS).
While ADAS features like Anti-lock Braking Systems (ABS) have been around for a longer time, the concept of driver assistance has been applied for even longer. As early as 1995, BMW introduced the Park Distance Control (PDC) system in the E38 model, which used ultrasonic signals to help drivers understand the distance between the vehicle and front and rear obstacles during parking, preventing collisions. This marked the beginning of the development of systems that actively influence driver control based on detected vehicle environment data.
Modern ADAS systems are generally divided into three parts: sensors, processors, and actuators. First, sensors such as cameras, radar, ultrasonic sensors, and even more expensive LiDAR are used to measure the distribution of the vehicle’s surrounding environment using light, images, and sound waves. These sensors are typically installed on the front and rear bumpers, windshield, and side mirrors, with the number of sensors depending on the vehicle’s ADAS configuration. According to the SAE International standard, the lowest level, Level 0, has no automated driving functions and only provides driving assistance information. For example, the commonly used Around View Monitoring (AVM) system only requires the installation of cameras and short-range radar.
ADAS is not synonymous with autonomous driving but is a prerequisite for achieving it. Processors and actuators play a crucial role in self-driving technology at Level 1 and above. In addition to displaying the sensor data for driver reference, the data is also transmitted to the processor, where the Electronic Control Unit (ECU) analyzes it and makes decisions, which are then transmitted to the actuators to control the throttle and steering wheel, enabling partial or fully automated vehicle control. For example, the Level 2 Automatic Parking Assist (APA) system only requires the driver to control the throttle, while the actuator operates the steering wheel.
Market sales data and public information show that Level 1 and Level 2 self-driving technologies will remain the mainstream for the next five years. Cameras and ultrasonic sensors are the primary components. Although cameras rely on software to simulate human visual perception to judge the environment, they are susceptible to weather and light conditions. However, compared to radar and LiDAR, cameras are less expensive and can be installed at multiple angles on the vehicle to obtain a complete view of the environment, making them the current mainstream configuration for ADAS.
Cameras provide image information and are therefore called image sensors (CIS: CMOS Image Sensor). The captured color image is divided into red, green, and blue pixels by a filter and enters the CIS. The CIS, based on its resolution and pixel design, has a corresponding matrix. Each pixel is a photodiode. When a photodiode receives light, it is converted into an electrical signal, which is transmitted through CMOS switches as an analog signal to the next component, the analog front-end (AFE), where it is converted into a digital signal and then processed by an image signal processor (ISP) to generate an image, which is then transmitted to the processor SoC (System on Chip) for calculation, judgment, prediction, and even learning. The conversion from analog to digital signals requires extremely fast speed and low interference, allowing the SoC to accurately interpret the data in real-time and provide the necessary parameters for the backend actuator to operate, assisting the vehicle in steering and power system driving.
CMOS Image Sensor and Signal Processing
With the rapid development of ADAS, there is a need for stable and fast electronic signal transmission. As the amount of information transmitted increases, more power is required. Since ADAS has multiple processors, such as PCIE Switch, Security ECU, etc., to avoid interference between different controllers when problems occur, each processor requires a separate power supply. Additionally, to meet the requirements of down-conversion and reducing electromagnetic interference (EMI) within a limited space, power supply circuits often use Power Management ICs (PMICs), which integrate DC/DC converters and low dropout regulators (LDOs) and have a smaller footprint. For example, as mentioned earlier, if the CMOS image sensor encounters problems with image acquisition due to freezing at low temperatures, a heater is used to heat the CMOS sensor, and the power for the heater needs to be provided by a boost converter. The boost converter uses MOSFETs as switching elements.
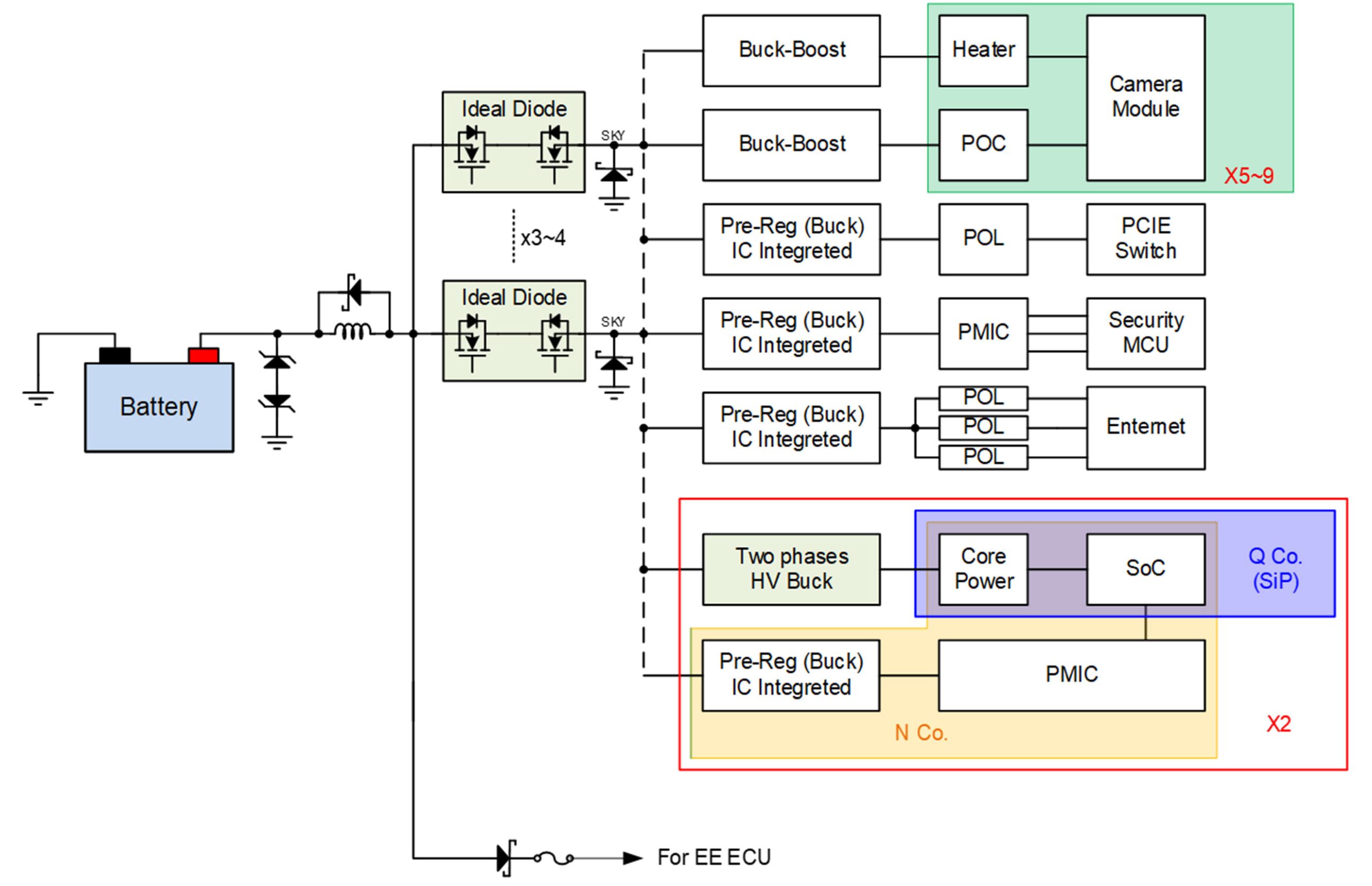
MOSFETs offer advantages such as fast switching speed, low power consumption, and high efficiency, making them ideal for ABS systems. They can quickly switch the pressure in the brake hydraulic system to adapt to changes in vehicle braking needs. Additionally, MOSFETs can effectively handle high currents and high-temperature environments, which is particularly important in automotive ABS systems.
The solenoid in the brake hydraulic valve body is controlled by the MCU in the ECU. In addition to the main control MOSFET, there are also freewheeling diodes used to protect the solenoid coil and control the application circuit. During braking, when the solenoid is energized, current flows through the solenoid coil, causing the valve to open and allowing hydraulic pressure to enter the valve body to apply braking force. However, when the solenoid is de-energized, the pressure in the hydraulic valve body is fixed, preventing continuous application of braking force and causing tire lockup. In the application circuit, due to the residual magnetizing current in the solenoid coil, a freewheeling diode is used to allow the current to decay smoothly, preventing the occurrence of voltage spikes and protecting the electronic devices in the circuit from damage.
Freewheeling diodes typically have high reverse voltage capability and high pulse current capability, enabling them to withstand the high voltage and high current operating environment of automotive ABS systems. Additionally, they have fast switching speeds and low forward voltage drop, reducing energy loss and ensuring efficient system operation.
Taiwan Semiconductor offers AEC-Q101 qualified PRD products. In addition, Taiwan Semiconductor can also provide customers with automotive-grade MOSFETs and TVS for ABS system protection devices to meet the requirements of automotive-specific test standards such as ISO 7637-2, ISO 10650, and ISO 16750-2.
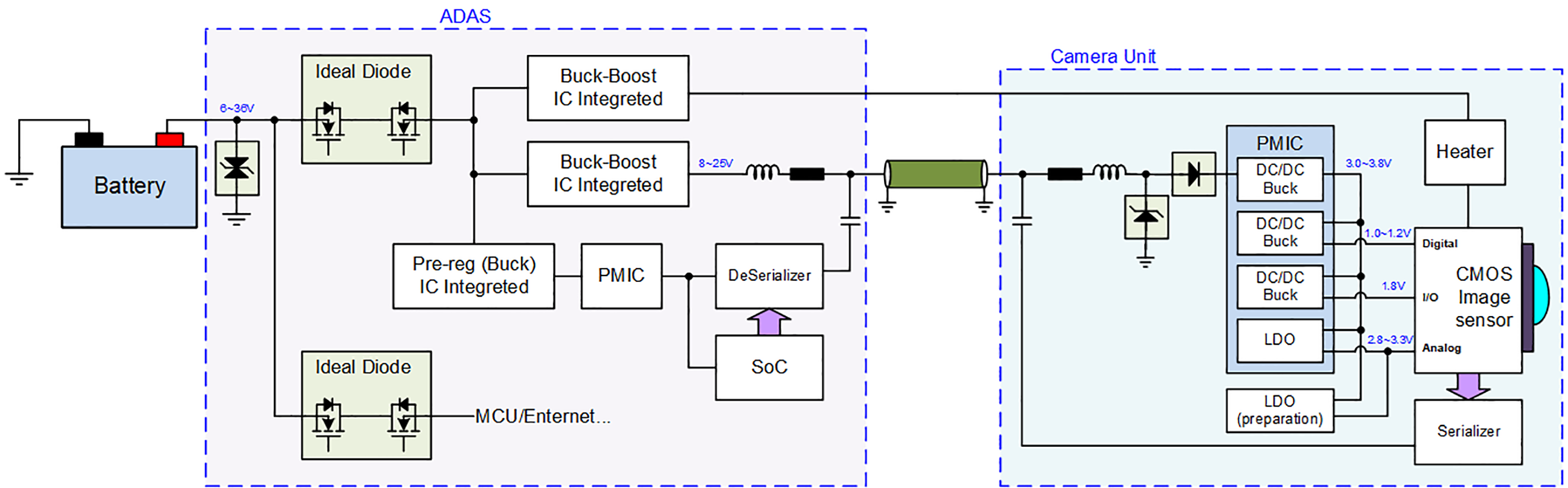
Power Management and Protection in ADAS
ADAS systems play a detailed and complex role in a vehicle’s electrical control system. To protect the circuit from transient overvoltage caused by events like lightning strikes or electrostatic discharge (ESD), it is essential to use TVS diodes for overvoltage protection. TVS diodes have a very low reverse breakdown voltage. When the voltage across the diode exceeds a certain threshold, it begins to conduct, limiting the voltage to the breakdown voltage of the TVS diode and protecting downstream circuits from damage.
TAIWAN SEMICONDUCTOR offers a range of automotive-grade PRD products that fully comply with the AEC-Q101 standard. Moreover, we can provide customers with AEC-Q101 qualified MOSFETs and TVS diodes for ABS system protection devices, meeting the stringent requirements of automotive-specific test standards such as ISO 7637-2, ISO 10650, and ISO 16750-2.
Products
Read more articles
- The Role of MOSFETs in Anti-lock Braking Systems (ABS)
- Powering the Electric Revolution: The Body Control Module (BCM) in Automotive
- Battery management system (BMS): Protecting and Managing Your Electric Vehicle
- Advanced LED Solutions for Enhanced Vehicle Visibility
- Power Components for On-Board Chargers (OBC): A Comprehensive Overview
- MOSFETs and Diodes: Key Components in Reverse Polarity Protection
- Sensor Fusion for Supplementary Restraint Systems (SRS)